摘要:在零件的數(shù)控加工中,對(duì)刀操作是基本要領(lǐng)。而深入認(rèn)識(shí)
對(duì)刀原理有助于編程加工的正確操作和相關(guān)參數(shù)的正確設(shè)置。本文以GSK980Tdb數(shù)控車床和Fanuc數(shù)控銑床為例,對(duì)控機(jī)床對(duì)刀原理作了理論上的探討和應(yīng)用舉例。
1.問題的提出在一次校企合作培訓(xùn)中,該公司大多數(shù)數(shù)控學(xué)習(xí)者知道數(shù)控機(jī)床對(duì)刀操作,但對(duì)數(shù)控機(jī)床對(duì)刀原理不知其所以然,有時(shí)出現(xiàn)一些莫名其妙的錯(cuò)誤,導(dǎo)致產(chǎn)品超差報(bào)廢。本文以數(shù)控車床和數(shù)控銑床為例,闡述有關(guān)數(shù)控機(jī)床對(duì)刀原理。
(1)數(shù)控車床對(duì)刀原理。對(duì)刀的目的是確定工件坐標(biāo)系與機(jī)床坐標(biāo)系的相互位置關(guān)系。工件裝夾在
機(jī)床上后,工件(工件坐標(biāo)系)的位置在機(jī)床坐標(biāo)系中是具體的,這一具體的位置是通過對(duì)刀操作來確定的。
因?yàn)榈段稽c(diǎn)的位置坐標(biāo)計(jì)算是以工件坐標(biāo)系(或編程坐標(biāo)系)的原點(diǎn)為參考來進(jìn)行計(jì)算的,而刀具的運(yùn)動(dòng)是以機(jī)床坐標(biāo)系的原點(diǎn)為參考的,如果刀具要有明確的運(yùn)動(dòng),就必須知道刀具的刀位點(diǎn)運(yùn)動(dòng)到給定的編程坐標(biāo)時(shí),相對(duì)應(yīng)的機(jī)床坐標(biāo)是多少。換句話來說,工件裝夾在機(jī)床上后,工件坐標(biāo)系相當(dāng)于機(jī)床坐標(biāo)系的一個(gè)子坐標(biāo),只有確定兩個(gè)坐標(biāo)之間的偏置關(guān)系,才能完成兩個(gè)坐標(biāo)系之間坐標(biāo)的轉(zhuǎn)換(將刀位點(diǎn)在編程坐標(biāo)系里的坐標(biāo)轉(zhuǎn)換成機(jī)床坐標(biāo)系里面的坐標(biāo)),刀具才有明確的運(yùn)動(dòng),而這一偏置關(guān)系是通過對(duì)刀來實(shí)現(xiàn)的。
以試切對(duì)刀為例,對(duì)GSK980Tdb數(shù)控車床對(duì)刀原理作一個(gè)簡(jiǎn)單的介紹。
如圖1所示,設(shè)刀具在X方向和Z方向的長(zhǎng)度分別為a、b(相對(duì)于刀架中心,a、b不一定要有確定的數(shù)據(jù)),試切外圓后刀具直徑為φ,X方向零點(diǎn)偏置為x(負(fù)值);試切端面后,Z方向零點(diǎn)偏置為z(負(fù)值)。
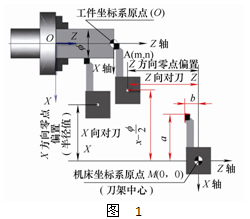
刀具運(yùn)動(dòng)到編程坐標(biāo)系原點(diǎn)時(shí)的機(jī)床坐標(biāo)為(2x―φ,z)(這一坐標(biāo)數(shù)據(jù)經(jīng)控制面板在刀補(bǔ)中通過輸入“Xφ”和“Zo”由數(shù)控系統(tǒng)自動(dòng)計(jì)算獲得并儲(chǔ)存),而工件坐標(biāo)系原點(diǎn)在機(jī)床坐標(biāo)系中的位置為(2x-φ-a,z-b)。
設(shè)工件坐標(biāo)系(或編程坐標(biāo)系)中刀位點(diǎn)任意一點(diǎn)的編程坐標(biāo)為A(m,n),則將此點(diǎn)坐標(biāo)轉(zhuǎn)換到機(jī)床坐標(biāo)系里面的坐標(biāo)為(2x-φ-a+m,z-b+n),而此時(shí)相應(yīng)的機(jī)床坐標(biāo)(刀架中心)為(2x-φ-a+m+a,z-b+n+b),即(2x-φ+m,z+n)(與刀具長(zhǎng)度無關(guān)),此時(shí)刀具有明確的機(jī)床運(yùn)動(dòng)坐標(biāo)。
所以對(duì)刀操作后,通過刀補(bǔ)的設(shè)定,便能確定任意刀具刀位點(diǎn)到達(dá)工件坐標(biāo)系原點(diǎn)時(shí)的機(jī)床坐標(biāo)(2x-φ,z),從而完成兩個(gè)坐標(biāo)系之間坐標(biāo)的轉(zhuǎn)換,并且確定相對(duì)應(yīng)的機(jī)床坐標(biāo),此時(shí)刀具有明確的機(jī)床運(yùn)動(dòng)。
(2)數(shù)控銑床對(duì)刀原理。數(shù)控銑床對(duì)刀原理和數(shù)控車床對(duì)刀原理相似,通過對(duì)刀確定工件坐標(biāo)系與機(jī)床坐標(biāo)系之間的空間位置關(guān)系,并將對(duì)刀數(shù)據(jù)輸入到相應(yīng)的存儲(chǔ)位置。
參考前述數(shù)控車床對(duì)刀原理可以看出,對(duì)刀操作的實(shí)質(zhì)是確定任意刀具刀位點(diǎn)到達(dá)工件坐標(biāo)系原點(diǎn)時(shí)的機(jī)床坐標(biāo),并記錄在機(jī)床里面,從而完成兩個(gè)坐標(biāo)系之間坐標(biāo)的轉(zhuǎn)換,并且確定相對(duì)應(yīng)的機(jī)床坐標(biāo),此時(shí)刀具有明確的機(jī)床運(yùn)動(dòng)。下面以Fanuc數(shù)控銑床XK7145A兩種情況為例,將工件坐標(biāo)系的原點(diǎn)設(shè)置在長(zhǎng)方體工件上表面的中心處(見圖2),簡(jiǎn)要介紹其對(duì)刀基本原理。
情景一:刀具裝上主軸對(duì)刀。先將機(jī)床參考點(diǎn)回零后,機(jī)床原點(diǎn)歸于正向極限位置。通過對(duì)刀后,機(jī)床坐標(biāo)顯示為(a,b,c),即各軸偏置量,如圖2a所示。刀長(zhǎng)為L(zhǎng),如圖2b所示,則工件坐標(biāo)系原點(diǎn)在機(jī)床坐標(biāo)系中的位置為(a,b,c-L)。
設(shè)任意編程坐標(biāo)為A(m,n,o),則將此點(diǎn)坐標(biāo)轉(zhuǎn)換到機(jī)床坐標(biāo)系里面的坐標(biāo)為(a+m,b+n,o+c-L),而此時(shí)相應(yīng)的機(jī)床坐標(biāo)(主軸端面中心)為(a+m,b+n,o+c-L +L),即(a+m,b+n,o+c)(與刀長(zhǎng)無關(guān)),此時(shí)刀具有明確的機(jī)床運(yùn)動(dòng)坐標(biāo)。
情景二:刀具不裝上主軸對(duì)刀(見圖3)。先將機(jī)床參考點(diǎn)回零后,機(jī)床原點(diǎn)歸于正向極限位置。通過對(duì)刀后,機(jī)床坐標(biāo)顯示為(a,b,c), 如圖3所示,即各軸偏置量,則工件坐標(biāo)系原點(diǎn)在機(jī)床坐標(biāo)系中的位置為(a,b,c)。
設(shè)任意編程坐標(biāo)為A(m,n,o),設(shè)刀長(zhǎng)為L(zhǎng),則將此點(diǎn)坐標(biāo)轉(zhuǎn)換到機(jī)床坐標(biāo)系里面的坐標(biāo)為(a+m,b+n,o+c),而此時(shí)相應(yīng)的機(jī)床坐標(biāo)(主軸端面中心)為(a+m,b+n,o+c+L)(與刀長(zhǎng)無有關(guān)),此時(shí)刀具有明確的機(jī)床運(yùn)動(dòng)坐標(biāo)。
此種情況對(duì)刀必須知道刀具長(zhǎng)度L,其長(zhǎng)度一般通過機(jī)外對(duì)刀儀對(duì)刀測(cè)量獲得。
2.數(shù)控銑床對(duì)刀應(yīng)用示例
現(xiàn)僅對(duì)數(shù)控銑床對(duì)刀應(yīng)用操作作一個(gè)示例介紹。
(1)對(duì)刀操作基本條件。①尋邊器,完成水平方向的對(duì)刀(見圖4)。②Z軸設(shè)定器,完成高度方向的對(duì)刀(見圖5)。
(2)對(duì)刀操作基本步驟。①將
尋邊器上、下部分人為稍偏心,裝于主軸。②選擇“MDI”操作方式,輸入“M03 S600”啟動(dòng)主軸正轉(zhuǎn)。③通過“手輪”(或“手動(dòng)”)模式使刀具靠近工件。④Y方向?qū)Φ?。⑤X方向?qū)Φ丁"轟方向?qū)Φ?。⑦檢驗(yàn)對(duì)刀的正確性。
Y方向?qū)Φ叮和ㄟ^調(diào)節(jié)手輪使尋邊器與工件一側(cè)面與刀具接觸,當(dāng)?shù)毒呓咏ぜr(shí),注意調(diào)整手輪的步距,選擇“×10”檔,當(dāng)尋邊器上下部分由偏心運(yùn)動(dòng)轉(zhuǎn)為同軸運(yùn)動(dòng)時(shí),其狀態(tài)由抖動(dòng)變?yōu)榻旗o止?fàn)顟B(tài),如圖6所示,此時(shí)認(rèn)為已找到該側(cè)面;按下“POS”鍵、軟鍵“相對(duì)”或“綜合”,輸入Y,按“歸零”軟鍵,如圖7所示;操縱主軸使尋邊器向上抬起,使之離開工件上表面一定距離,通過操作手輪使尋邊器與工件另一側(cè)面接觸,找正判別方法與上述相同,如圖8所示;記下CRT上顯示的“現(xiàn)在位置(相對(duì)坐標(biāo))”下的Y值,計(jì)算出Y1=Y/2;操作手輪,Z軸抬刀,再沿Y方向移動(dòng)工作臺(tái)至CRT上顯示的“現(xiàn)在位置(相對(duì)坐標(biāo))”下的Y值為Y1的位置,如圖9所示;在G54(注意:必須與加工程序中的選擇工件坐標(biāo)系指令一致)下設(shè)置Y值;按MDI鍵盤上的“OFFSET SETTING”鍵,按“坐標(biāo)系”軟鍵,進(jìn)入坐標(biāo)系參數(shù)設(shè)定界面(見圖10、圖11),用方位鍵“↓”將光標(biāo)移至G54坐標(biāo)參數(shù)設(shè)定區(qū),將光標(biāo)移至Y的坐標(biāo),輸入Y0, 按“測(cè)量”軟鍵。
X方向?qū)Φ叮篨方向?qū)Φ兜牟僮鬟^程類似于Y方向的對(duì)刀過程,不再贅述。
Z方向?qū)Φ叮孩僦鬏S不轉(zhuǎn),將Z軸設(shè)定器置于工件上表面,如圖12所示。②操作手輪,使刀具與軸設(shè)定器心軸的上表面剛好接觸,燈亮(見圖13)即停止刀具Z向運(yùn)動(dòng)。③在G54下設(shè)置Z值:按MDI鍵盤上的“OFFSET SETTING”鍵,按“坐標(biāo)系”軟鍵,進(jìn)入坐標(biāo)系參數(shù)設(shè)定界面,用方位鍵↓將光標(biāo)移至G54坐標(biāo)參數(shù)設(shè)定區(qū),將光標(biāo)移至Z的坐標(biāo),輸入(Z0- Z軸設(shè)定器的高度值),按“測(cè)量”軟鍵。
如果沒有
Z軸設(shè)定器的情況下,可以采取試切工件上表面的方法,即讓刀具轉(zhuǎn)動(dòng),在工件上表面輕輕刮起一層切屑為找正標(biāo)準(zhǔn),再輸入Z0即可)。
檢驗(yàn)對(duì)刀的正確性:①X、Y坐標(biāo)檢驗(yàn):操作手輪使刀具在Z方向離開工件上表面一定的距離;選擇MDI模式;按下PROG鍵;輸入“G54 G00 X0 Y0 ;”;按下“循環(huán)啟動(dòng)”按鈕,觀察刀具是否到達(dá)(X0,Y0),到達(dá)設(shè)定位置,說明對(duì)刀正確,否則錯(cuò)誤。②Z坐標(biāo)檢驗(yàn):操作手輪使工件遠(yuǎn)離機(jī)床主軸軸線。選擇MDI模式;按下PROG鍵;輸入“G54 G01 Z0 F300 ;”;按下“循環(huán)啟動(dòng)”按鈕,注意觀察刀具下降的過程,如果刀位點(diǎn)到達(dá)設(shè)定的Z0位置后停下來,說明對(duì)刀正確,如果刀具端面超過工作上表面而未停止,立即按下“急停”按鈕。
3.結(jié)語(yǔ)
通過以上內(nèi)容的探討,使操作者對(duì)數(shù)控機(jī)床對(duì)刀操作有一個(gè)深刻的認(rèn)識(shí),使操作者在設(shè)置刀補(bǔ)和靈活處理尺寸公差時(shí)有據(jù)可依,從而避免了尺寸超差,保障了公司產(chǎn)品質(zhì)量。
(本文刊登于《金屬加工(冷加工)》雜志2015年第23期,作者單位:廣東理工職業(yè)學(xué)院,中山金屬制品有限公司 )